5 materiais de construção inovadores que preservam o meio ambiente
Confira alternativas para driblar os principais impactos ambientais da obra, como o descarte de resíduos, o uso de fontes não-renováveis, a emissão de gases poluentes e o desmatamento
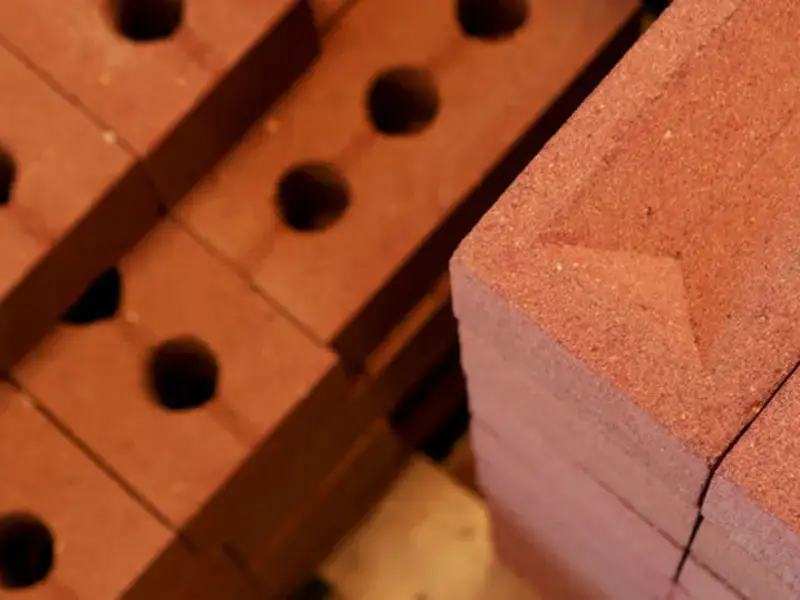
Você já deve ter ouvido que a indústria da construção civil é considerada uma das mais agressivas ao meio ambiente. Parte deste impacto ambiental se deve aos resíduos de obras e demolições, na maioria, não-degradáveis ou de difícil degradação.
Segundo dados da ABRECON (Associação Brasileira para Reciclagem de Resíduos da Construção Civil e Demolição), o Brasil gera aproximadamente 84 milhões de m³ desses resíduos.
Pelo próprio padrão construtivo brasileiro, o maior percentual de descarte é o de argamassa (63%), seguido de concreto e blocos (29%). Ainda mais preocupante que o lixo doméstico, este resíduo da construção civil representa um grande volume para os aterros sanitários. Um material difícil de ser compactado e degradado, que contribui para esgotar rapidamente o espaço disponível.
Para reverter a situação, o arquiteto Vitor Penha, do Estúdio Penha, acredita que o agente da transformação precisa ser o profissional da área. “É papel dos arquitetos apresentar alternativas ecológicas aos moradores”, explica.
Para além dos resíduos das obras, a crescente demanda por sustentabilidade deve englobar outros prejuízos do nosso método construtivo, incluindo o amplo uso de fontes não-renováveis, a emissão de gases poluentes e o desmatamento.
Confira abaixo cinco alternativas que podem ser o futuro de quem se preocupa com o meio ambiente!
Tijolo reciclado
/i.s3.glbimg.com/v1/AUTH_a0b7e59562ef42049f4e191fe476fe7d/internal_photos/bs/2023/B/N/qtq9RBSXAK8OIF7wgzoQ/tijolo-sustentavel.jpg)
Quer solução mais óbvia para os resíduos de construção do que aproveitá-los para criar novos materiais? Batizado de K-Briq, o tijolo sustentável desenvolvido pela brasileira Gabriela Medero, na Universidade Heriot-Watt de Edimburgo, na Escócia, possui 90% de sua matéria-prima reciclada. A criação rendeu à profissional um lugar na lista Top 50 Women in Engineering (WE50).
Outro bônus é que a peça não é queimada, evitando a emissão de gases poluentes, outro impacto preocupante do setor. Segundo relatório publicado pelo Programa das Nações Unidas para o Meio Ambiente em 2020, a construção civil e sua indústria são responsáveis por 38% das emissões de dióxido de carbono (CO₂).
“Este é o primeiro tijolo do mundo feito com 90% de resíduos de construção e demolição. Ele é produzido com um décimo das emissões de gás carbônico, usando menos que um décimo da energia necessária para a fabricação de um tijolo tradicional”, afirma Gabriela. “Além disso, produzimos os tijolos em uma instalação de reciclagem de resíduos, reduzindo os km de transporte”, completa.
Blocos de sururu
/i.s3.glbimg.com/v1/AUTH_a0b7e59562ef42049f4e191fe476fe7d/internal_photos/bs/2023/K/z/D1NMW8TryPjmmR932zsQ/cobogo-feito-com-casca-de-sururu-e-reconhecido-em-premio-internacional3.jpg)
A relação do designer Marcelo Rosenbaum com o sururu começou em 2019, quando, a convite do Instituto Brasileiro de Desenvolvimento e Sustentabilidade (IABS Brasil) e da Prefeitura de Maceió, ele apresentou alternativas para o aproveitamento das 300 toneladas de conchas descartadas mensalmente.
O cobogó de sururu da Mundaú, desenvolvido em parceria com o Estudio Rodrigo Ambrosio e o mestre artesão Itamácio Alexandre do Vergel, venceu o prêmio IF Design 2022 – considerado o Oscar do design de produtos e de interiores.
Atualmente, o item é produzido pelo Instituto A Gente Transforma, com apoio do departamento de Engenharia Civil da Universidade Federal de Alagoas (UFAL), e comercializado pela marca Portobello.
O próximo passo é levar ao mercado os blocos de sururu, uma alternativa aos tijolos comuns feitos de argila, um recurso finito, extraído da natureza, que utiliza combustível fóssil em sua queima. “Este processo gera um excesso de emissões de gases de efeito estufa, e libera monóxido de carbono e outros poluentes atmosféricos”, explica Marcelo. “Os blocos ecológicos de sururu serão produzidos no canteiro de obras, utilizando o mínimo possível de cimento em composição com o solo local e o resíduo da concha de sururu triturada”, complementa.
Cimento comestível
/i.s3.glbimg.com/v1/AUTH_a0b7e59562ef42049f4e191fe476fe7d/internal_photos/bs/2023/W/8/mFDFtbRWWua8AI4DugWQ/conheca-o-cimento-comestivel-material-inovador-que-utiliza-residuos-alimentares-na-construcao-civil-2.jpg)
Pesquisadores da Universidade de Tóquio, no Japão, desenvolveram uma técnica por meio da qual é possível produzir cimento a partir de resíduos alimentares, como folhas de repolho, cascas de laranja, cebola e banana. Além de alcançar a resistência necessária para a construção civil, o material é literalmente comestível.
A técnica envolve cortar os alimentos, secá-los em uma estufa, pulverizá-los, misturar com água, para, então, prensá-los a altas temperaturas. Todo o processo de fabricação foi documentado no artigo Development of Novel Construction Material from Food Waste.
Além de resistência e flexibilidade, o material foi testado nos quesitos sabor e aroma. “Nosso objetivo era usar algas marinhas e restos de comida comuns para criar materiais que fossem, pelo menos, tão fortes quanto o concreto”, conta Yuya Sakai, autor do estudo e engenheiro especializado em concreto e reciclagem. “Mas, como já estávamos usando resíduos de alimentos comestíveis, também achamos interessante determinar se o processo de reciclagem impactaria o sabor dos materiais originais”.
Com exceção do cimento de abóbora, todos os materiais foram aprovados no teste de resistência, com destaque para o de repolho, que se mostrou três vezes mais forte que um concreto comum. Já o sabor e o cheiro permaneceu estável pelos quatro meses, resistindo a fungos e insetos. Um dos colaboradores do projeto criou a marca Fabula Inc., que produz utensílios domésticos e outros artigos em cimento comestível. O uso como material de construção ainda requer mais estudos antes seguir para o mercado.
Madeira plástica
/i.s3.glbimg.com/v1/AUTH_a0b7e59562ef42049f4e191fe476fe7d/internal_photos/bs/2023/8/M/oMEstSRze425Q9rBlwCQ/madeira-plastica.jpg)
O desmatamento é outro impacto ambiental conhecido da construção civil. Isso porque a madeira é uma matéria-prima muito apreciada pelos brasileiros, empregada em revestimentos internos, externos e no mobiliário.
Segundo Marcelo Mujalli, presidente da Associação Brasileira de Designers de Interiores (ABD), há uma tradição no país de que a madeira está relacionada com conforto, sofisticação e elegância. Além disso, a durabilidade e a sua fácil adaptação com qualquer estilo são outros fatores que chamam a atenção.
Uma alternativa ainda pouco difundida no Brasil é a madeira plástica, também conhecida como madeira sustentável. Trata-se de um material produzido com resíduos plásticos de alta densidade, que oferecem muita resistência, durabilidade e reduzem os custos com manutenção.
A Reset, primeira fábrica de madeira ecológica da América Latina, tem uma produção anual que ultrapassa 2,5 mil toneladas de madeira plástica por ano. “São aproximadamente 3,2 bilhões de sacos de salgadinhos e outras embalagens, que se tornam 70 mil metros quadrados produzidos de madeira plástica. A utilização de polipropileno reciclado como matéria-prima para a produção da madeira ecológica, permite preservar mais de 4 mil árvores adultas a cada ano”, afirma o fundador Cadu Ristum.
Granilite sustentável
/i.s3.glbimg.com/v1/AUTH_a0b7e59562ef42049f4e191fe476fe7d/internal_photos/bs/2023/H/0/oQkQ20SzmsKxvR4Pjnog/terrazzo-sustentavel.jpg)
Direto da década de 1980, o granilite parece ter reencontrado seu espaço no design de interiores. Na linha do upcycling, o designer londrino Robin Grasby usa sobras de mármore para criar uma espécie de terrazzo, que ele descreve como “bem caótico”, mas que, sem dúvida, tem seu charme. Batizado de Altrock, o material pode ser usado para bancadas, revestimentos, mesas e ladrilhos, e o melhor – cada peça é única!
Feito com 87% de materiais reciclados, ele leva farinha de mármore (basicamente, o pó que resulta do corte do mármore), lascas, pedaços de sobra e lajes quebradas dessa rocha. Os outros 13% correspondem a resina, para unir tudo. O material resultante é moldado à mão e pode ser pigmentado em cores personalizadas para projetos sob medida. Ele ainda é selado com óleo de cera para resistir às manchas.
“Eu queria desenvolver algo a partir do mármore, que pudesse mostrar a beleza desse material e utilizar suas propriedades como uma superfície resistente, mas de uma maneira única e contemporânea”, explica Grasby.
Mais do que o revestimento em si, a ideia de usar o máximo de sobras e resíduos na fabricação de um revestimento igualmente belo pode ser facilmente adaptada in loco.