Especialistas apresentam tendências e inovação digital
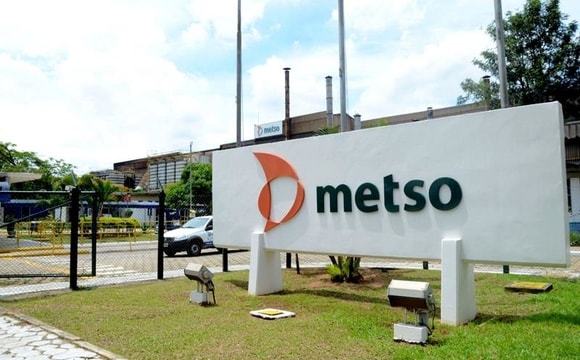
A digitalização avança no setor de mineração e pode ser adotada em etapas, de acordo com cada cenário. Essa constatação foi apresenta em evento ocorrido em Belo Horizonte no início de novembro último que reuniu cerca de 200 profissionais de mineração – quatro deles internacionais – que participaram de uma maratona de 16 palestras para apresentar o que vem ocorrendo desde a mina até a planta de processamento.
A edição 2018 do Seminário Internacional Metso (SIM) teve um recorde de inscrições e metade das vagas foram preenchidas em 24 horas. “A palavra de ordem do evento foi digitalização, mas a senha, sem dúvida, é compartilhamento e co-criação de soluções”, resume Marcelo Motti, vice-presidente da Metso.
Segundo ele, a digitalização está na agenda de todos os CEOs de mineração e a companhia resolveu mostrar como está inserida nessa onda de mudança. Para entender as novidades que o SIM 2018 trouxe, veja o roteiro abaixo:
Metais têm futuro: Para o consultor George Hemingway, sócio da consultoria norte-americana Stratalis, o consumo de metais têm futuro em função de várias iniciativas como a reciclagem e novos tipos de exploração, inclusive submarina. Mas a mineração que vai sobreviver é aquela que for rápida e flexível. Segundo ele, a indústria tradicional pode aprender com a disrupção, mas o foco não é a tecnologia em si, mas os novos modelos de negócios. Assim como o Uber é um serviço de transporte sem ter veículos, é possível que mineradoras do futuro não tenham os ativos, mas negociem os metais. Para Hemingway, a digitalização é uma realidade, mas não é suficiente porque o cenário de mudanças envolve várias indústrias, então todas são afetadas. Otimista, ele acredita que o setor tenha capacidade de mudar, mas lembra que ele deve enfrentar o futuro, conhecer os “desmancha-prazeres”, que podem atrapalhar a transição e se preparar para mudar o eixo, se for o caso. Entre as estratégias, estão o uso da infraestrutura para criar benefícios, ser inteligente a respeito da velocidade de adoção das mudanças e considerar que uma ajuda adicional, ou seja, especialistas, pode ser necessária.
Digitalização agrega inteligência ao processamento mineral: Para Jani Puroranta, diretor de Digitalização da Metso, o processamento mineral ganha inteligência com três iniciativas: estabilização (reduz-se a variabilidade dos processos), otimização (aumenta a taxa de produção) e maximização (maior disponibilidade dos ativos e aumento da produtividade). Essas etapas, de acordo com ele, são necessárias para que o setor mineral enfrente os desafios atuais como a demanda de energia elétrica (a mineração sozinha consome cerca de 4% da energia do mundo) e a movimentação de materiais (em média para cada 3 milhões de toneladas aproveitadas, o setor movimenta 250 milhões de toneladas). Puroranta avalia que a mineração no futuro será uma operação muito mais integrada da mina ao porto, com ganhos ao longo da cadeia, operação remota e mínima intervenção humana. Do ponto de vista da manutenção, o aumento da disponibilidade será uma realidade se a digitalização for bem-feita. As razões? De novo, a colaboração entre especialistas das mineradoras e dos parceiros, dividindo informações em tempo real e resolvendo juntos os problemas de operação e manutenção.
Compartilhamento é a palavra chave para eficiência energética: Sul-africano baseado na universidade australiana de Queensland, Dr. Grant Ballantyne é um exemplo da colaboração em pesquisa na área de eficiência energética. Ele é integrante do Coalition for Eco-Efficient Comminution (CEEC), iniciativa que envolve o compartilhamento de experiências entre vários especialistas mundiais e participou de projetos reais em minas como a Sunrise Dam, da Anglo American Ashanti, na Austrália, e na mina de prata de Saucito, da Fresnillo, no México, entre outras. Ou seja, combina pesquisa e aplicação prática. É com esse background que ele estima três horizontes tecnológicos para eficiência energética – now, near e next. No primeiro, as ações são fáceis de serem implementadas, mas têm grande impacto. Os resultados podem variar entre 5% e 50% de eficiência energética. No segundo, o foco são tecnologias que também são relativamente fáceis de serem ativadas, mas que demandam capital, com uma otimização complementar entre 15% e 30%. O terceiro cenário de horizonte tecnológico envolve melhorias ainda mais significativas, com aplicação de múltiplas tecnologias, e otimização entre 40% e 60%.
Mineração de dados ou dados da mineração? Resposta: ambos. A mineração de dados é um termo comum em tecnologia da informação (TI), mas no caso do setor mineral, também estamos falando de dados do setor e de uma visão integral, que começa na caracterização do minério, antes mesmo do processamento, e nas melhorias que podem ser feitas com o cruzamento de informações de campo, com testes em laboratório e com o uso de experiências anteriores. Essa é, resumidamente, a base da Geo-metalurgia automatizada, apresentada pela consultora australiana Suzy Lynch Watson, da Metso. Ela mostrou como é possível combinar cenários de otimização, com dados em tempo real. Um exemplo é o uso de tags desde a etapa de desmonte de rocha e passando por toda a britagem. Pense neles como sensores móveis e remotos que acompanham o minério e informam sobre o teor da rocha que vai entrar na planta de processamento, entre outros dados. A especialista coordena um grupo mundial de profissionais da Metso, inclusive Brasil, que estão desenhando a usina autônoma do futuro.
Rastreamento do minério em tempo real: O uso de tags para rastrear o minério processado é um dos recursos da geo-metalurgia automatizada. São vários tipos de tags que podem ser colocados no furo dos desmontes e que seguem o mesmo percurso do minério em todo o processamento de britagem. Como são georreferenciados, ou seja, sabe-se exatamente onde eles foram colocados nos blocos de rocha desmontados, é possível identificar, na prática, quando um minério de qualidade ou outro de baixo teor está entrando no processamento. Já adotado no Brasil, o uso de tags melhora quando integrado a outras tecnologias.
Usina autônoma: Ela já existe no Brasil e trata-se de uma jornada modular que envolve a aplicação de várias tecnologias também comprovadas em campo. A primeira mudança na adoção da usina autônoma é cultural e implica a criação de um planejamento, diminuindo a intervenção humana e instalando sensores que permitem o auto-ajuste da planta. Apesar de modulares, as ferramentas se integram, permitindo que os processos possam ser otimizados e a operação maximizada, incluindo redução de consumo energético. A combinação de informações da mina complementa a automação da planta, principalmente porque leva a ajustes finos quando um minério de alto ou de baixo teor entra na usina.
Serviços 4.0 marcam os novos tempos: imagine uma parada programada anual da planta. Agora pense que a paralisação será gravada em detalhes para a otimização das futuras paradas e que todo o processo pode ser acompanhado – online – por um aplicativo, indicando número de pessoas envolvidas na manutenção e status do processo. Pois bem, esses são alguns dos recursos já existentes em que devem ser disponibilizados em breve pela Metso. Como cada minuto de parada conta, a ideia da empresa é estreitar o processo, mas sem comprometer a confiabilidade e segurança.
Viabilizando a mineração de ferro de menor teor: Apesar de o Brasil ser um dos mais importantes players da produção de minério de ferro do mundo, o país também tem operações com baixo teor, o que exige processamento com baixo custo operacional e maior produtividade. Esse é o foco do uso da prensa de rolos (HRC) apresentada no SIM 2018. A tecnologia vem sendo aperfeiçoada pela Metso e levou a uma redução drástica do consumo de energia em relação a sistemas tradicionais de cominuição, sendo de cinco a sete vezes menor. Com a solução é possível moer o minério de ferro até uma condição em que ele possa ser processado com baixo custo. Além do custo operacional, a adoção do HRC também leva a um investimento menor de capital.
Britagem na cava ganha espaço: Conhecida em inglês como InPit Crushing, a britagem na cava teve seu ápice na mídia com a instalação do maior britador de mandíbula sob esteiras, feito pela Metso no Cazaquistão em 2012. O interessante é que o conceito de InPit Crushing pode ser concretizado na forma móvel, semi-móvel e, inclusive fixa. No Brasil, a empresa negocia a ativação de um modelo similar ao instalado no Cazaquistão, mas com capacidade ainda maior. Entre os ganhos do sistema está a eliminação da frota de caminhões na mina, com redirecionamento da mão de obra, eliminação de contaminantes, como gases e lubrificantes, e maior lucratividade.
Nova geração de peneiramento ultrafino: A tecnologia de peneiramento ultrafino já existe, mas o diferencial da Metso foi reduzir pela metade o espaço necessário para instalação do equipamento – em relação aos hidrociclones tradicionais – e melhorar o desempenho, processando com entre 15% e 20% a menos de carga circulante. A mineradora também pode optar pela melhoria da eficiência energética, conseguindo uma redução também entre 15% e 20%. Os números são uma média da tecnologia e cuja nova geração entrou oficialmente no mercado no ano passado. No Brasil, ela já tem operação comercial, comprovando que pode aumentar a capacidade operacional e reduzir o espaço necessário no design da planta.
Prensa de rolos reduz energia e aumenta produtividade: as melhorias da prensa de rolos HPGR em um caso real de mineração de cobre nos Estados Unidos mostraram que é possível replicar o sucesso da tecnologia no Brasil. O equipamento, que faz parte da linha de frente de inovações recentes da Metso reduziu o consumo de energia em 10% na média e levou a um aumento de produtividade de cerca de 20%. O desenvolvimento levou em consideração as deficiências técnicas de modelos concorrentes e apostou nos testes exaustivos de laboratório tanto no Brasil como nos Estados Unidos.
Maior segurança na troca de revestimentos em moinhos: a solução apresentada pela Metso reduz a possibilidade de acidentes na troca de revestimentos internos de moinhos. A redução de pessoas na zona de risco foi conseguida com um novo sistema de fixação dos revestimentos – pela parte externa do moinho com uso de parafusos invertidos. A nova tecnologia também eliminou a necessidade de maçaricos e outros equipamentos. Um ganho adicional é a diminuição do tempo de parada na operação.
Fonte: EAE Máquinas